Industrial refrigeration systems are important for many industries, including food processing and chemical manufacturing. These systems help keep temperatures just right to ensure that perishable items stay safe and fresh and to support various industrial processes that need specific conditions. But how do these large cooling systems work? In this article, we will learn how a refrigeration system functions by looking at its main parts and explaining how they work together to provide effective and dependable cooling.
What is a Refrigeration System?
A refrigeration system is a process that takes heat away from a specific area to make it cooler. In industries, these systems are very important for keeping temperatures low for storage, manufacturing, or processing. They use a substance called refrigerant, which is a special chemical that absorbs heat from the surroundings and moves it elsewhere, usually outside the building.
While the basic idea is straightforward, the design and operation of these systems are much more complicated than those of regular home refrigerators. Industrial systems require larger, more precise, and more durable equipment to meet specific needs, which is why they have unique features that set them apart.
Key Components of a Refrigeration System
An industrial refrigeration system has several important parts that work together to keep temperatures low. Each part has a specific job, and the whole system needs regular maintenance to run efficiently.
1. Compressor
The compressor is the main part. It circulates the refrigerant, which is a special fluid used for cooling. The refrigerant starts as a gas and is pulled into the compressor, where it gets pressurized and heated. This high-pressure gas then moves on to the next step in the cooling process. Industrial compressors are much larger and stronger than those in home refrigerators and come in different types, like screws, reciprocating, and centrifugal compressors.
2. Condenser
After the refrigerant is pressurized by the compressor, it goes to the condenser. In the condenser, the high-pressure gas cools down and turns into a liquid. This process releases the heat that the refrigerant picked up earlier. The condenser is usually located outside the building so it can easily release heat into the air or water around it.
3. Expansion Valve
The expansion valve is a key part that controls how the refrigerant flows into the evaporator. When the high-pressure liquid refrigerant passes through this valve, it experiences a big drop in pressure. This drop causes the refrigerant to expand and cool down quickly, getting it ready for the next step in the cooling cycle.
4. Evaporator
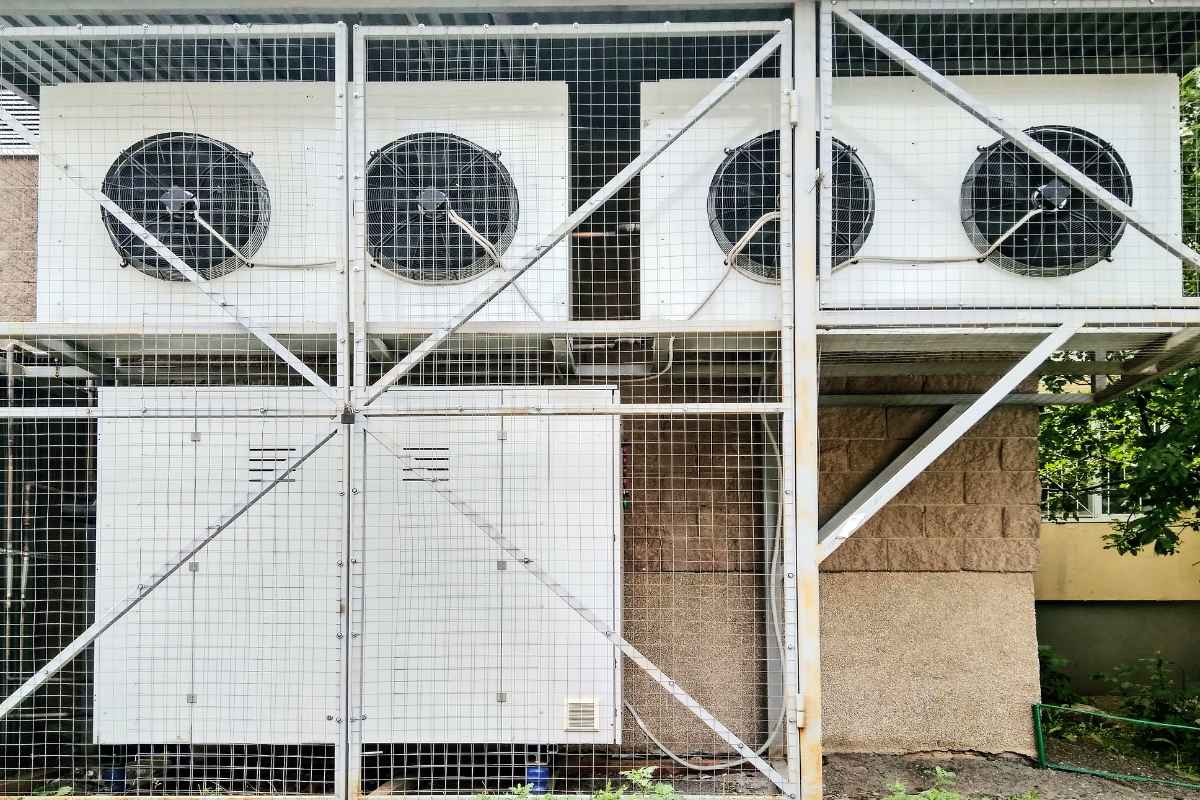
The evaporator is where the actual cooling takes place. The low-pressure, cold refrigerant absorbs heat from the surrounding area, like a storage room or production space. As it absorbs heat, the refrigerant evaporates and turns back into a gas, completing the cycle. In industrial settings, evaporators are often large coils or plates that maximize the surface area for heat exchange.
The Refrigeration Cycle
Now that we’ve talked about the main parts, let’s go through the entire refrigeration system cycle step by step:
- Compression Stage: The compressor takes in low-pressure refrigerant gas and squeezes it into a high-pressure, high-temperature gas.
- Condensation Stage: The compressed gas then goes to the condenser, where it releases heat and turns into a high-pressure liquid.
- Expansion Stage: The high-pressure liquid refrigerant passes through the expansion valve, where it loses pressure and temperature.
- Evaporation Stage: The cold, low-pressure liquid refrigerant enters the evaporator, where it absorbs heat from the surrounding area, turns it into a gas, and goes back to the compressor to start the cycle all over again.
This closed-loop system works very efficiently, helping industrial facilities keep the low temperatures they need for their operations.
Types of Refrigeration Systems
Different industries need various types of systems based on the size of their facilities, the products they store or process, and their specific cooling requirements. Here are some of the most common types:
1. Ammonia Refrigeration Systems
Ammonia is a popular refrigerant in industrial refrigeration because it is very efficient and has a low impact on the environment. These systems are often used in large food processing plants, cold storage facilities, and beverage industries. Ammonia systems are especially effective for operations that need very low temperatures.
2. CO2 Refrigeration Systems

Carbon dioxide (CO2) is another eco-friendly refrigerant used in industrial refrigeration. It has a much lower potential for global warming compared to traditional refrigerants like CFCs or HFCs. CO2 refrigeration is commonly found in places that need efficient cooling, such as supermarkets, large food production facilities, and ice rinks.
3. Cascade Systems
A cascade system is a type of industrial refrigeration that uses two different refrigerants in separate stages of the cooling process. These systems are perfect for applications that require ultra-low temperatures, like pharmaceutical manufacturing and cryogenic storage. The cascade setup helps maintain high efficiency, even at very low temperatures.
Applications of Industrial Refrigeration
These systems are used in many industries where controlling temperature is crucial for keeping products safe, maintaining quality, and ensuring efficient processes. Here are some important applications:
1. Food and Beverage Industry
The food and beverage industry is one of the biggest users of industrial refrigeration. These systems are key for keeping perishable items fresh, managing fermentation processes, and freezing products for long-term storage. From dairy products to frozen foods, it is vital for food safety and extending shelf life.
2. Pharmaceutical Industry
In the pharmaceutical field, maintaining precise temperatures is crucial for making and storing sensitive drugs and vaccines. These systems are used in manufacturing plants, research labs, and cold storage areas to protect the quality of pharmaceutical products.
3. Chemical and Petrochemical Industries
In the chemical and petrochemical industries, controlling temperatures is important for ensuring product quality and safety. These systems help cool reactors, store volatile chemicals, and safely handle materials that are sensitive to temperature changes.
4. Cold Storage Warehouses
Cold storage warehouses depend on large industrial refrigeration systems to keep the right temperatures for storing perishable goods. These facilities are used by various industries, including agriculture, food distribution, and pharmaceuticals.
Benefits of Industrial Refrigeration Systems
1. Energy Efficiency
Modern systems are designed to use less energy, which helps businesses save on costs and reduce their impact on the environment.
2. Precision Temperature Control
These systems come with advanced controls that allow for very precise temperature management. This is important in industries where even small temperature changes can affect product quality.
3. Scalability
These systems can be customized and adjusted to fit the needs of any facility, whether it’s a small operation or a large production plant.
4. Durability
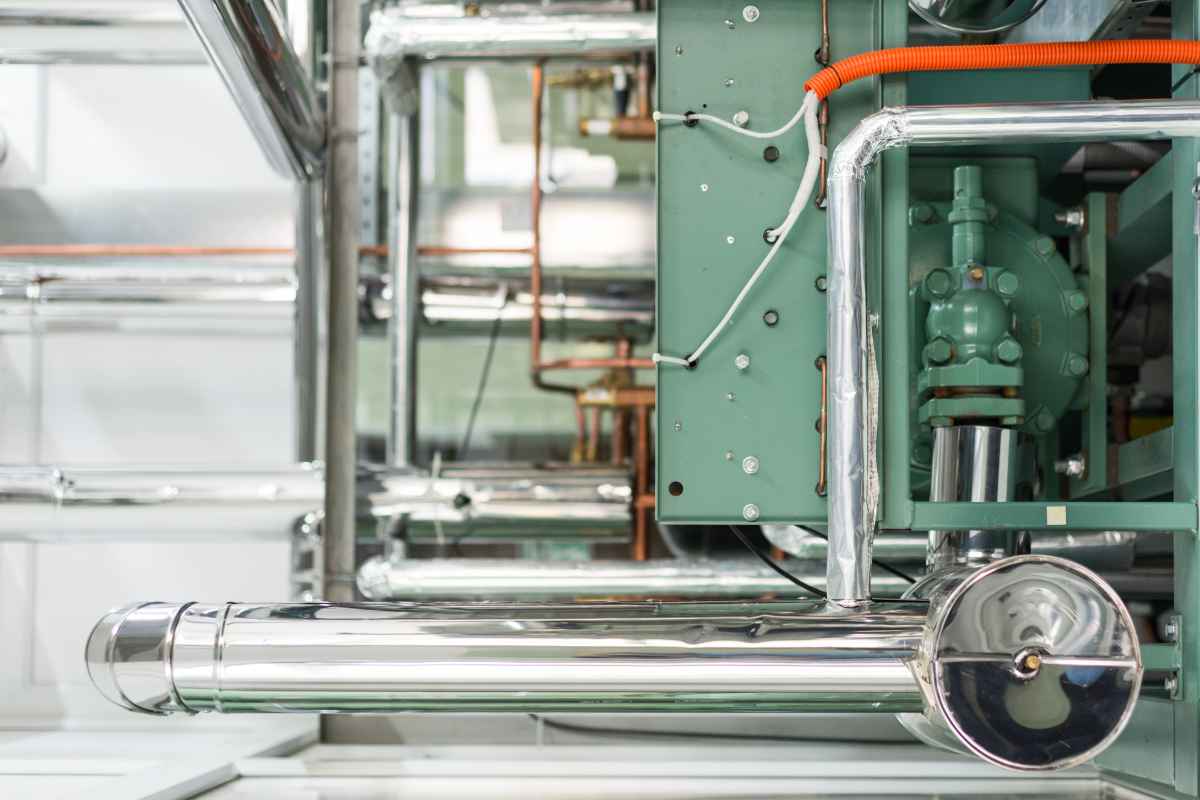
The equipment used in industrial refrigeration is built to be strong and long-lasting. It is made from tough materials and designed to handle harsh industrial conditions and continuous use.
The Future of Industrial Refrigeration
As industries focus more on being sustainable and using energy efficiently, the future of industrial refrigeration is shifting towards using more eco-friendly refrigerants and smarter control systems.
New developments in refrigerant technology are leading to the creation of refrigerants that have a lower impact on global warming, which will help make these systems even more environmentally friendly. Additionally, the use of the Internet of Things (IoT) and artificial intelligence (AI) technologies is expected to enhance system performance, lower energy use, and improve maintenance by predicting when repairs are needed.
Conclusion
Industrial refrigeration systems are necessary for keeping products safe and to maintain its high quality in many industries. Over time, businesses can improve how they manage and maintain their cooling systems for better efficiency by learning how these systems work and what parts they include.
Also Read: How Cloud Computing Is Revolutionising the Public Transportation Industry?